Grason
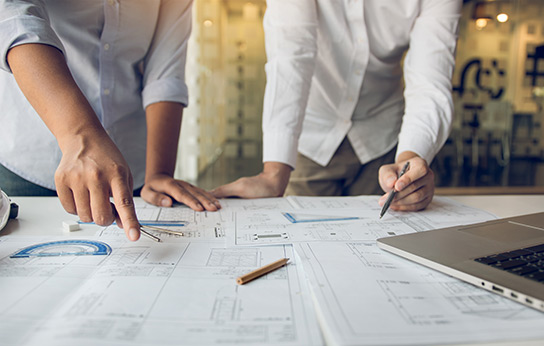
About us
Standards and credentials
We visualize and design our devices in CAD 3D technology using the CAD Inventor® program.
Design process
1. FIRST CONTACT WITH THE CLIENT
A new Client is first contacted via e-mail or by phone. After initial verification of the Client’s requirements, we provide a budget bid that covers our capacities and the scope of offered work.
2. SITE VISIT
The next stage involves a visit of our specialists at the Client’s site in order to get study the mixer’s target operating location and the available utilities required to supply the machine. We are also happy to welcome the Client at our company and enable familiarization with the plant.
3. ENGINEERING WORK
After verification and concluding the contract, we commence engineering work. Each component and device proposed by us or the Client will be designed and visualized in CAD 3D using the CAD Inventor® software.
4. PRE-MANUFACTURING ACCEPTANCE
Prior to manufacturing, the proposed design must be approved by both sides. We commence further work only upon passing this stage.
5. ORDERING MATERIALS AND MANUFACTURING
The Manufacturing Department launches the material procurement process and places orders with subcontractors. Most elements are made on CNC machines – starting with laser sheet metal cutting, through bending, rolling and machining. Our designs are virtually unique and most of them are custom-tailored to the Client’s needs, which is why welding follows the manual TIG method.
6. PROGRAMMING
When the device is in production, the Instrumentation and Control Department develops its part of the design. Control, which is the construction of a control cabinet with equipment and programming are conducted entirely in-house. Developing the software and touch-panel visualization is not limited to applying ready-made patterns but is always approved by Client and verified in line with the Client’s demands.
7. CONNECTING ELEMENTS
The ultimate, most important stage is “hooking-up” all elements together, which is the interconnection of cooperating mechanical and electrical parts of the device.
8. DEVICE START-UP AND TESTS
The most anticipated moments are the device start-up and testing of its functions. After testing and trials, the QC Department approves the mixer for further commissioning work.
Conducted tests:
– surface roughness tests,
– pressure and tightness tests, if required,
– VT2 100% visual inspection of welding connections,
– operating temperature accuracy test,
– control functional tests.
All tests and trials are conducted using measuring instruments legalized and calibrated by a third-party laboratory.
9. TECHNICAL ACCEPTANCE AND TRAINING
After successful testing, we invite the Client to participate in the technical acceptance and verification against the placed order. We conduct FAT (Factory Acceptance Test) and SAT (Site Acceptance Test) at the Client’s premises. They are aimed at the functional verification of the mixer and its system against the assumptions. By default, we train the technical personnel that will operate the device.
10. IQ AND OQ QUALIFICATIONS
In the case of pharmaceutical plants, after successful FATs and SATs, we shall commence IQ Qualification (Installation Qualification), which is the confirmation of the correct installation and an approval of element conformity with the requirements and design, followed by Operation Qualification (OQ), which involves checking the correctness and functional accuracy of the device and its components.